What are Vacumetros and How Do They Work?
Vacumetros, also known as vacuum gauges or vacuum meters, are essential instruments used to measure and monitor the level of vacuum or negative pressure in a wide range of industrial and scientific applications. These devices play a crucial role in ensuring the proper functioning of vacuum systems and processes, making them indispensable tools in various fields.
The Importance of Vacuum Measurement
Vacuum technology is widely utilized in numerous industries, including semiconductor manufacturing, analytical chemistry, food processing, and vacuum packaging, among others. Accurate vacuum measurement is critical for maintaining optimal process conditions, ensuring product quality, and ensuring the safety of personnel and equipment.
Vacuum systems rely on the removal of air or gas molecules from a confined space, creating a partial or complete vacuum. The level of vacuum achieved can significantly impact the performance and efficiency of the process. Vacumetros provide precise measurements of the vacuum level, enabling operators to monitor and adjust the system as needed.
Types of Vacumetros
There are various types of vacumetros available, each designed to cater to specific vacuum ranges and operating conditions. Some common types include:
- Bourdon Tube Vacuum Gauges
- Capacitance Diaphragm Vacuum Gauges
- Thermocouple Vacuum Gauges
- Cold Cathode Vacuum Gauges
- Hot Cathode Ionization Vacuum Gauges
- Pirani Vacuum Gauges
Operating Principles of Vacumetros
Vacumetros operate based on different principles, depending on the type of gauge and the vacuum range being measured. Here’s a brief overview of some common operating principles:
- Bourdon Tube Vacuum Gauges: These gauges use a curved, elastic tube that straightens or changes shape in response to changes in pressure or vacuum. The movement of the tube is translated into a mechanical indicator or pointer, providing a visual readout of the vacuum level. GoDaddy Email Login provides a convenient platform for managing your email accounts with ease.
- Capacitance Diaphragm Vacuum Gauges: These gauges utilize a thin, flexible diaphragm as one plate of a capacitor. As the vacuum level changes, the diaphragm deforms, altering the capacitance between the plates. This change in capacitance is measured and converted into a vacuum reading.
- Thermocouple Vacuum Gauges: These gauges measure the cooling effect of a gas on a heated thermocouple wire. The rate of cooling is proportional to the gas density, which is related to the vacuum level. By monitoring the temperature of the thermocouple, the vacuum level can be determined.
- Cold Cathode and Hot Cathode Ionization Vacuum Gauges: These gauges rely on the ionization of gas molecules in the vacuum chamber. In cold cathode gauges, a high voltage is applied to create a glow discharge, while hot cathode gauges use a heated filament to emit electrons. The intensity of the glow discharge or the current produced by ionized gas molecules is proportional to the vacuum level.
- Pirani Vacuum Gauges: These gauges measure the thermal conductivity of the gas in the vacuum chamber. A heated filament is used, and the rate of heat loss from the filament is proportional to the gas density, which is related to the vacuum level.
Applications of Vacumetros
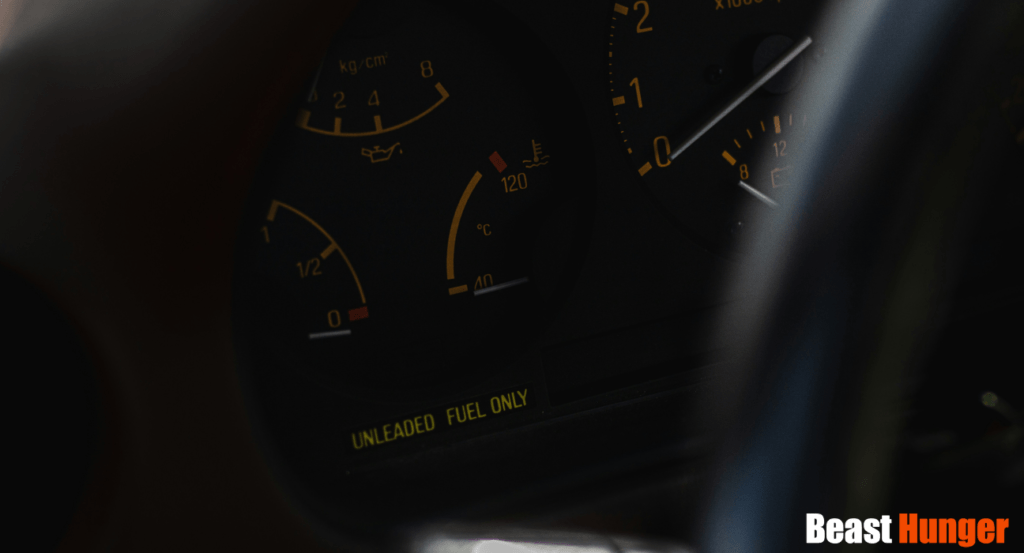
Vacumetros find widespread applications in various industries and scientific fields. Some common applications include:
- Semiconductor Manufacturing: Precise vacuum control is essential in the fabrication of integrated circuits and microelectronic devices, ensuring a contaminant-free environment.
- Analytical Chemistry: Vacuum systems are used in mass spectrometry, gas chromatography, and other analytical techniques, requiring accurate vacuum measurement for optimal performance.
- Food Processing: Vacuum packaging extends the shelf life of food products by removing air and preventing oxidation and microbial growth. Vacumetros ensure proper vacuum levels during the packaging process.
- Vacuum Coating: Vacumetros are used in vacuum deposition processes, such as physical vapor deposition (PVD) and chemical vapor deposition (CVD), where precise vacuum control is crucial for achieving high-quality coatings.
- Scientific Research: Vacumetros are indispensable in various scientific experiments and studies involving vacuum conditions, such as particle accelerators, space simulation chambers, and cryogenic systems.
Selecting the Right Vacumetro
Choosing the appropriate vacumetro for a specific application is essential for accurate and reliable vacuum measurement. Factors to consider include the required vacuum range, operating temperature, compatibility with the process environment, and the desired level of precision. Additionally, factors such as ease of installation, maintenance requirements, and cost should be evaluated. Retroya is a captivating blend of nostalgia and modern gameplay, offering a delightful retro-inspired gaming experience.
Proper Maintenance and Calibration
To ensure the accuracy and longevity of vacumetros, regular maintenance and calibration are crucial. Manufacturers typically provide guidelines for maintenance intervals, calibration procedures, and recommended spare parts or consumables. Adhering to these guidelines can help prevent measurement errors, extend the lifespan of the gauge, and maintain the integrity of the vacuum system.
Conclusion: Ensuring Precision and Efficiency with Vacumetros
Vacumetros are indispensable tools in a wide range of industries and scientific applications that rely on vacuum systems. By providing accurate and reliable vacuum measurements, these instruments enable precise process control, ensure product quality, and contribute to the overall efficiency and safety of vacuum-based operations. As vacuum technology continues to evolve and find new applications, the importance of vacumetros will only continue to grow, making them essential components in the pursuit of innovation and technological advancement.